Grand Seiko is no stranger to groundbreaking, sometimes industry-shattering, innovations. This is, after all, the company which in 1969 sparked the quartz crisis when it unveiled the Quartz Astron—a watch so precise that it nearly undid the livelihoods of Swiss mechanical watchmakers. That is, of course, its most famous claim to fame in its constant strive for accuracy. Decades later, when mechanical watchmaking was experiencing a renaissance, its engineers came out with the first production-level capacity Spring Drive—the world’s most accurate self-winding or manual winding watch movement—which combines elements of both mechanical and quartz precision. That technology was conceived in 1999 and debuted in a very limited run of watches as a test-run before it hit full production five years later. Now, the brand has unveiled several next-level innovations in the T0 concept movement: The brand’s first tourbillon, the world’s first integrated constant force mechanism and tourbillon, and the most accurate, purely mechanical watch it has ever made, accurate to within less than half a second per day. How is that for a triple whammy? For the record, there is nothing that comes close to that level of accuracy in the mechanical watchmaking industry to date.
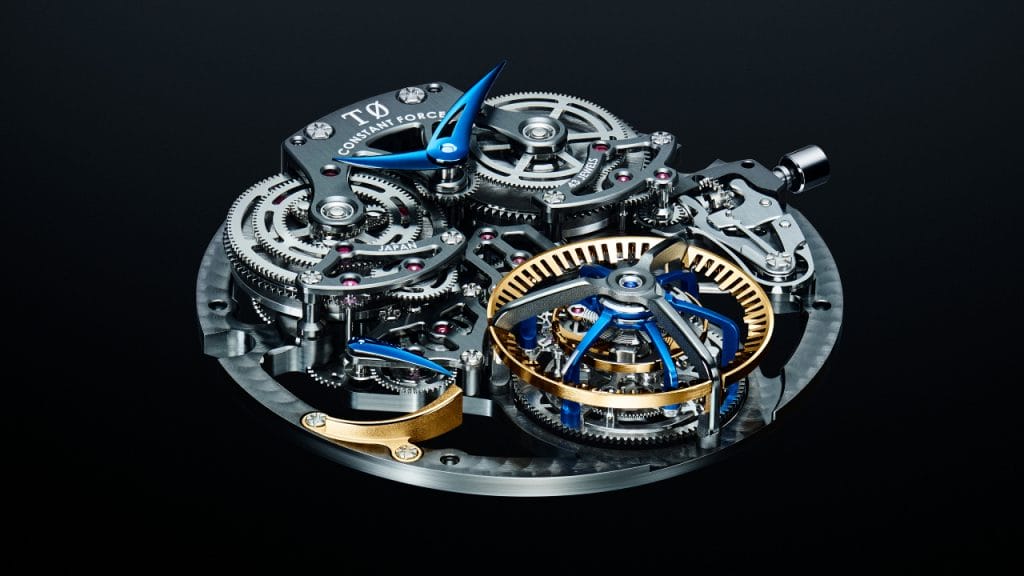
The constant force mechanism, which delivers constant energy whether the power reserve is low or high, coupled with the tourbillon, which rotates the escapement around to prevent errors from gravity, integrated together on the same axis creates a remarkably accurate timepiece. This configuration has never been seen before. Essentially, they work on the same plane, which maximises energy efficiency.
There are Swiss watchmakers, like Arnold & Son and IWC, that have created watches with both a constant force mechanism and tourbillon (although it’s a rare occurrence), but melding the two together is an entirely new achievement. Part of the difficulty lies in the manufacturing capabilities and skill level needed to create this kind of movement. Combine that with the challenge of making parts in the right shapes and sizes to integrate these two technically challenging complications, along with the painstaking design it entails, and you have one very intricate movement. To create the parts, Grand Seiko used its proprietary MEMS (Micro Electro Mechanical Systems) manufacturer, which makes the micron-level tolerance components used for all the wheels and gear trains.
The company also created new hardening coatings, which are also semi-lubricating, for the metal wheels. It sounds very similar to a Roger W. Smith project which plans to use a nano-material to coat metal wheels that reduce the need for oil lubrication, which eventually has to be replaced by a servicing department. (And metal wheels are more durable than the fragile silicon components adopted by watch brands in recent years.) Traditional watchmakers like Smith, as well as F.P. Journe, have been working on side-stepping silicon to work with traditional metal while developing techniques that eliminate oil. It has yet to be incorporated for metal components, in a production wristwatch.
Grand Seiko also used ceramic for the first time on the stop wheel, also developed to withstand micron-level tolerances, which is visible at 6 o’clock. The company says it has been running the T0 movement for a year and has seen no fracturing or chipping of the component. The tourbillon cage, the little arms in blue also at 6 o’clock, has been crafted from titanium anodic oxidation to create a film on the outside, instead of using paint or electroplating, meaning its hue is everlasting. The wheel at 6 o’clock is the constant force mechanism, while the white tab on the blue arm is the deadbeat seconds counter, meaning it jumps from second to second. The three arms of the outer carriage show the one-second interval of the delivery of energy, while the lower axis rotates at 4 Hz frequency or 28,800 beats per hour, the highest frequency of any tourbillon.
The free-sprung, three-armed balance wheel is also a unique shape, never before seen in any Grand Seiko caliber. Unlike the 9SA5 Hi-Beat, launched earlier this year, this model uses a rotatable nut instead of screws to change the speed. But in case your head is already spinning from the technical details, there are a couple of poetic ones to note as well. The wheels in the gear train have a pinwheel design with comma-like arms inspired by the Shinto shrines of Japan. The shape is called the “Tomoe,” derived from an old family crest expressing a whirlpool. It’s an East Asian nod to the tourbillon, which is French for whirlwind.
But unlike the silent zen-like tranquility of the Spring Drive movement, the T0 has a constant force mechanism that clicks once per second, while the 4 hz beat of the frequency creates what the brand calls the “16th Note Feel,” spelled out on the back of the movement, to create a sound akin to a minute tambourine shake.
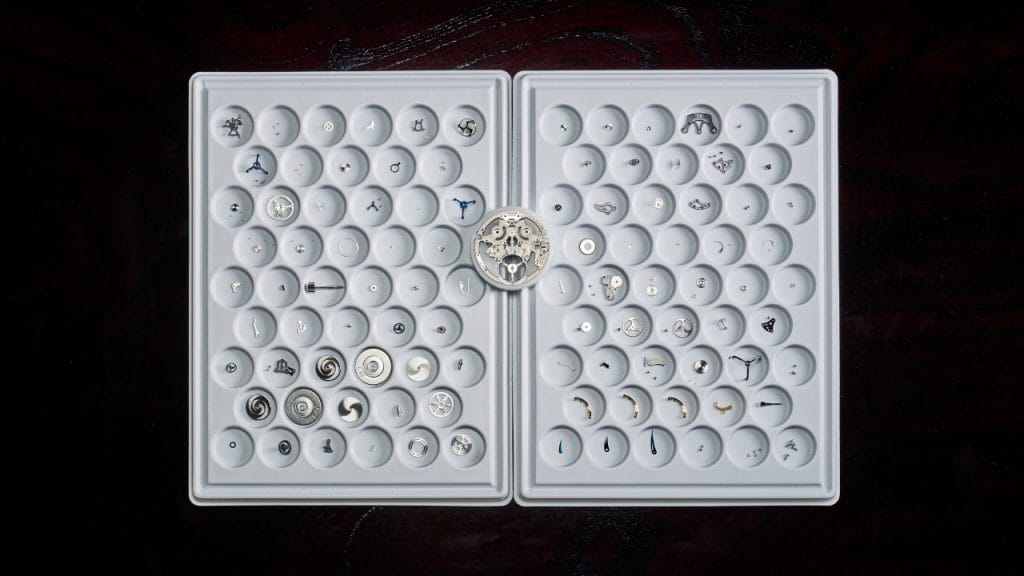
Finally, the piece is entirely hand-finished, a process that takes three months. Everything from these decorative elements to its technical prowess was achieved in the brand’s new Grand Seiko studio in Shizukuishi unveiled in mid-July. The movement will be on display in the building’s second-floor lounge overlooking Mt. Iwate, the source of inspiration for many Grand Seiko watches.
In sum, the T0 is a very costly endeavor, which is why it’s not in production…yet. The T0 concept movement has been secretly under development for the last 7 years—most production movements take 3 years on average. So, while Grand Seiko says it doesn’t currently have plans to incorporate it in a wristwatch, you can bet the amount of time and money poured into the R&D for this movement, designed by Takuma Kawauchiya, suggests that there are definitely big plans for it in the future. In fact, the concept was being conceived at the same time the company was working on its recently released 9SA5 model, so that innovations in each one helped push the other along. Some of the capabilities of T0 that were incorporated into the 9SA5, including the free-sprung balance and MEMS manufacturing method.
It should be seen as a signal of big things to come in elevating the Grand Seiko brand into the realm of haute-horology, much like its hard-to-find elevated sister brand Credor, but with more technical innovation. Back in October 2019, when we visited both the Credor Micro Studio and the Grand Seiko manufacturer in Japan, Seiko Holdings’ president, COO and CMO Shuji Takahashi, alluded to high-end developments coming for the Grand Seiko brand.
“The challenge,” he told Robb Report is continuing to seek a balance not only between the European and Japanese traditions, but also between Seiko’s two increasingly respected brands.” He added that Grand Seiko would always be grounded in functionality and Credor in artistry, but, he asked himself, ‘Would a Grand Seiko ever have a tourbillon?’ He danced around a yes, saying that this was always the philosophical debate between the two brands. Eleven months later, we have his answer. Now, you just have to wait for one for your wrist.
Previously published in Robb Report.