In the later half of the 19th century, the Industrial Age was in full swing. An enterprising young American watchmaker, Florentine Ariosto Jones, sought to partake in the ongoing revolution by starting his own manufacture. He settled on the city of Schaffhausen, in northeastern Switzerland. It was a well-connected trading hub on the River Rhine, with established infrastructure including a railroad and a hydropower dam (courtesy of a certain Heinrich Moser). And, believe it or not, at the time Swiss labour was considered low-cost. Jones thus founded the International Watch Company in 1868.

Jones was evidently not possessed of long-term ambition, as by 1880 he had ceded the company’s ownership to Swiss industrialists. But the groundwork he had laid, and his original vision of combining traditional craftsmanship with the latest in industrial advancements would stand the company in good stead. The International Watch Company, better known today as IWC Schaffhausen, would go on to become a prominent horological force. The 20th-century wartime era would see the manufacture distinguish themselves with military and pilot’s watches, while the post-war years saw innovations such as Albert Pellaton’s revolutionary, highly efficient bidirectional winding system, and the first Ingenieur with its anti-magnetic shielding. The 1970s would reveal the iconic Gerald Genta-designed Ingenieur SL, while the 1980s found Kurt Klaus developing his perpetual calendar system which would raise the bar in terms of simplicity and user-friendliness.
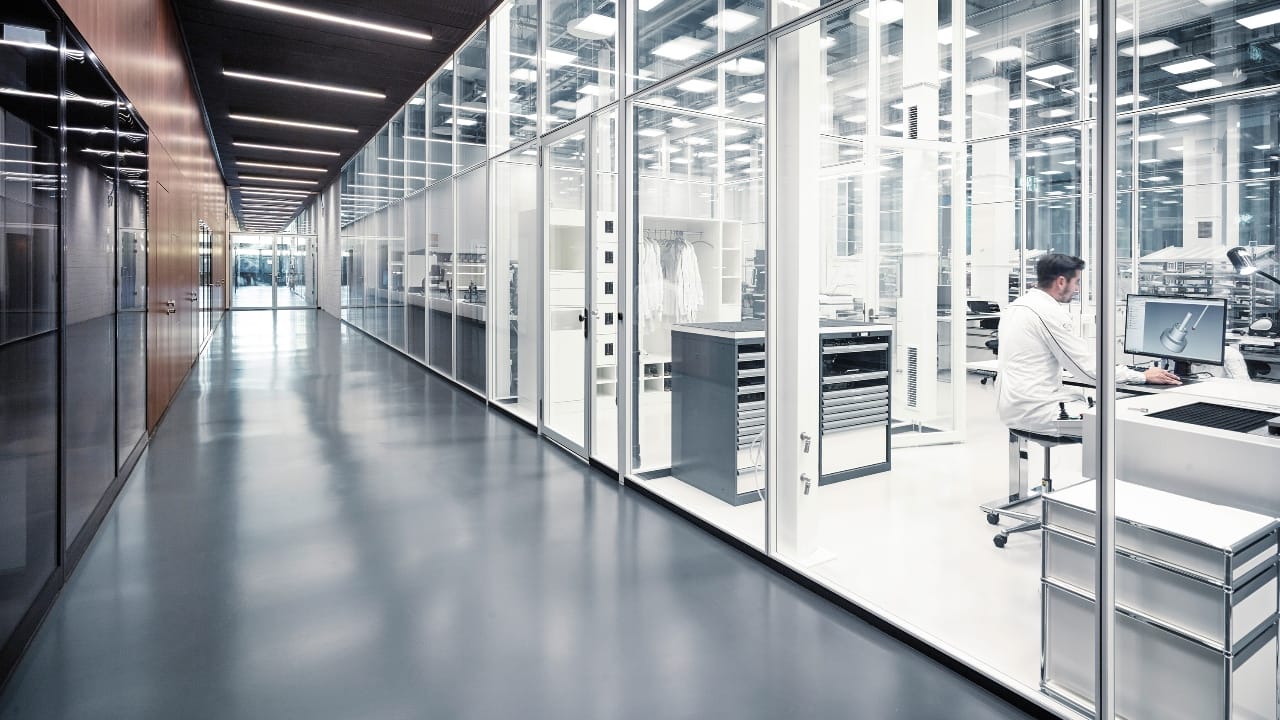
Through the decades, IWC never budged from its Schaffhausen home. Situated in the middle of town and a stone’s throw away from many Renaissance-era landmarks, the original building was completed in 1875. It sits right on the bank of the River Rhine, only a few kilometres upstream from the Rhine Falls, the most powerful waterfall in Europe. Today, the building serves as headquarters and R&D centre; it also has a boutique and museum on the ground floor, along with a watch restoration and service workshop.
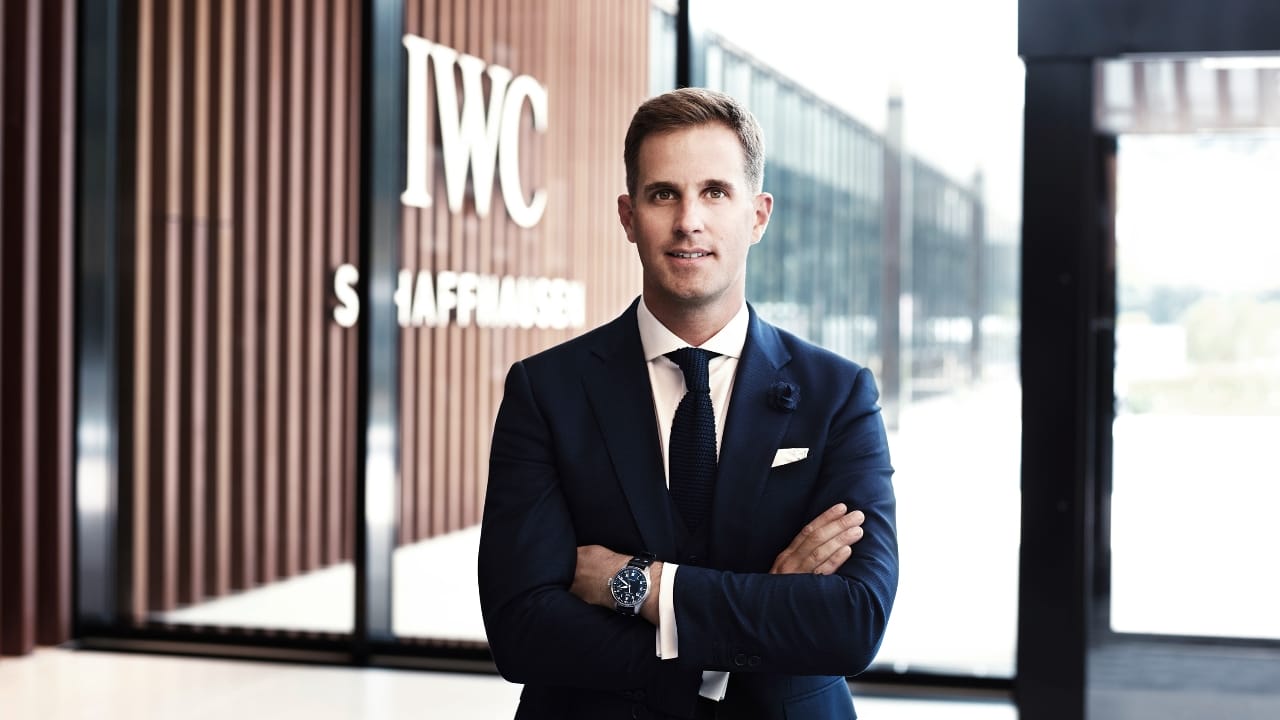
These days, the watchmaking proper is conducted a little further away, to the tune of a 10-minute drive. On the outskirts of Schaffhausen—but still officially in Schaffhausen, and not some neighbouring district, which was an important factor in choosing the site—is the new IWC Schaffhausen manufacture. Inaugurated in 2018, it is a modern, purpose-built facility that allowed the brand to consolidate the watchmaking process. The CHF42 million, 13,500sqm manufacture—or manufakturzentrum, one could say, as Schaffhausen is in the German-speaking region of Switzerland—has allowed the brand to unite movement and case component production and assembly under one roof for the first time. Christophe Grainger-Herr, the CEO of IWC Schaffhausen, is an architect by training and was a key part of the design process before he took on his current role in 2017. His inspiration was modernist exhibition pavilions, places where people of industry, trade and art would gather to showcase their best. The result is clean lines, high ceilings and open spaces with long sightlines that seem to invite visitors to enter and have a look around. The manufacture currently has about 230 employees, but was built with expansion in mind and can therefore support up to 400. An efficient layout was a design priority, and it shows in the way each step of the process flows linearly and seamlessly into the next—from raw bars of metal to milling and machining, to decoration, all the way to dust-free cleanrooms where assembly takes place. One of Grainger-Herr’s more idiosyncratic decisions was to have all the various industrial machinery painted white, rather than being left in their original various colours as they typically are. It gives the manufacture an especially organised, uniform look.
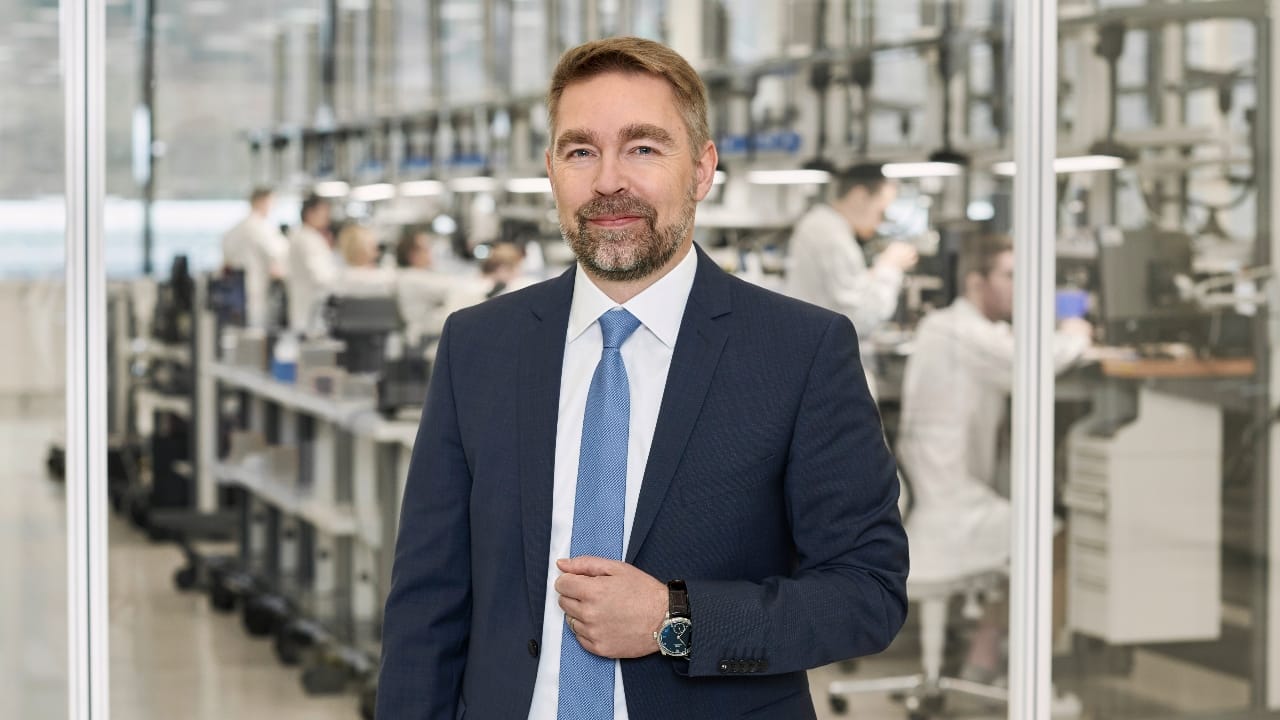
Stefan Ihnen, Associate Director of R&D at IWC Schaffhausen, adds that the new manufacture is a great improvement over the old, rather fragmented setup that meant people or components sometimes having to go to another building entirely. “It’s really a significant advancement in communication, enabling different areas to engage more directly,” he explains. “We can organise side-by-side shop floor meetings and be more efficient and cohesive.”
While Ihnen is a frequent visitor to the manufakturzentrum, his department remains based in the original headquarters in Schaffhausen’s town centre—one big advantage, he says, is that this allows him to take quick lunchtime walks along the river. Research and development has historically been a key part of IWC Schaffhausen, and it continues to embrace its technical nature. “We are proud of our engineering heritage, with research and development playing a pivotal role. The creation of new products, especially movements, is essential for us. In recent years, development of these movements has been increasingly important,” Ihnen explains, adding that one part of the new building is dedicated to movement development.
A veteran at IWC Schaffhausen of more than two decades, Ihnen has witnessed some of the more memorable developments, including the Big Pilot’s Watch Shock Absorber XPL, an eight-year project that can survive accelerations of over 30,000g; the development of Ceratanium, a proprietary material that combines the lightness and toughness of titanium with the scratch-resistance of ceramic; and the Tribute to Pallweber Edition ‘150 Years’, a wristwatch homage to the original digital display pocket watch of 1885. He started at IWC as a movement developer. “Over the past 10 to 15 years, we have developed a huge number of base movements,” he says. “This has brought us to a position where all movements are IWC manufactured—which has been quite a challenge.”
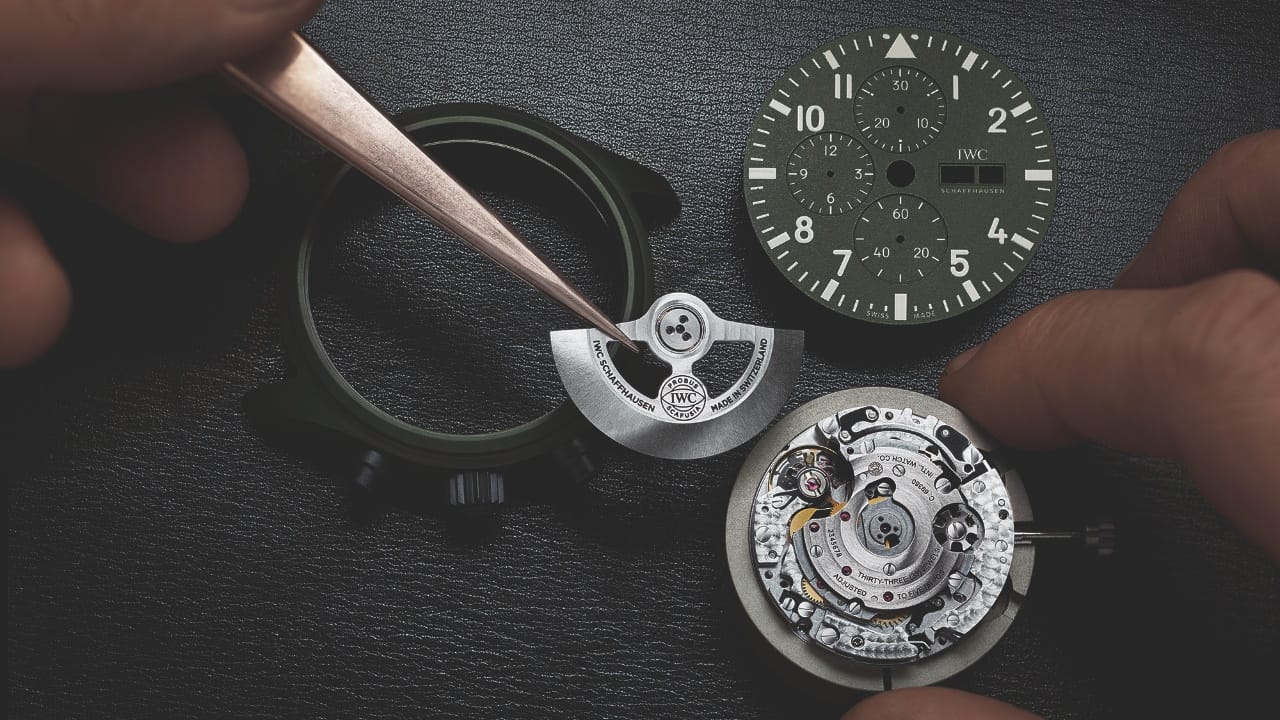
Ihnen originally trained as a watchmaker before picking up a degree in precision engineering. The combination of watchmaking and engineering capabilities is extremely sought-after in his department, and most of his colleagues have a similar skillset. “You can be a good engineer, but without the specific watchmaker background, it’s pretty hard—it takes quite a long time to train them,” he says. The modern engineering context involves a large degree of electronics, IT and similar high-tech fields, but watchmaking is a specific and anachronistic mechanical discipline. “An engineer comes with a good background in how to structure a product, how to develop specific solutions to technical problems and so on. So the combination is ideal,” he explains.
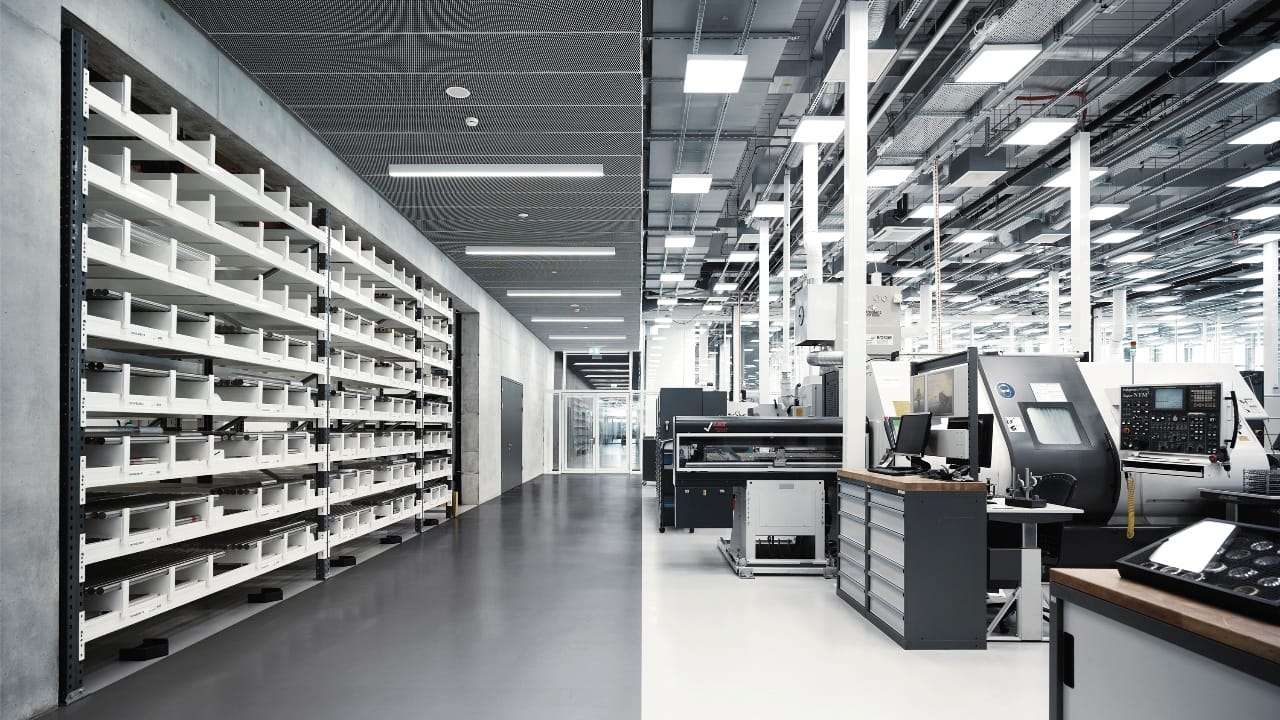
One unique challenge Ihnen faces is the relative difficulty of attracting talent to the Schaffhausen, in the German-speaking part of Switzerland, when most of the industry is based in the western, French-speaking areas. “It’s only 100km away, but it’s really a different mentality, a different language,” says Ihnen, who himself is a native of Germany. “We are one of the biggest watch producers in the German-speaking part of Switzerland. We are really a bit apart from other brands in the western part,” he adds. “I believe what sets us apart is our unique heritage. We had an American founder with a vision of industrialisation. This differentiates us. Although we also have complications, our approach is always grounded in engineering—we prioritise problem-solving, readability and precision. We don’t create complications for the sake of it—instead, every complication is designed with a purpose, to solve a specific problem.”